Material Selection in Production, Construction and Life Cycle
A proper calculation and comprehensive planning also consider the factors of material selection. A presentation using the example of aluminium, steel and glass-fibre reinforced plastics (GRP) for side walls, roofs and floors of commercial vehicles and mobile homes is intended to provide information about the return on investment in vehicle construction.
What is Return on Investment?
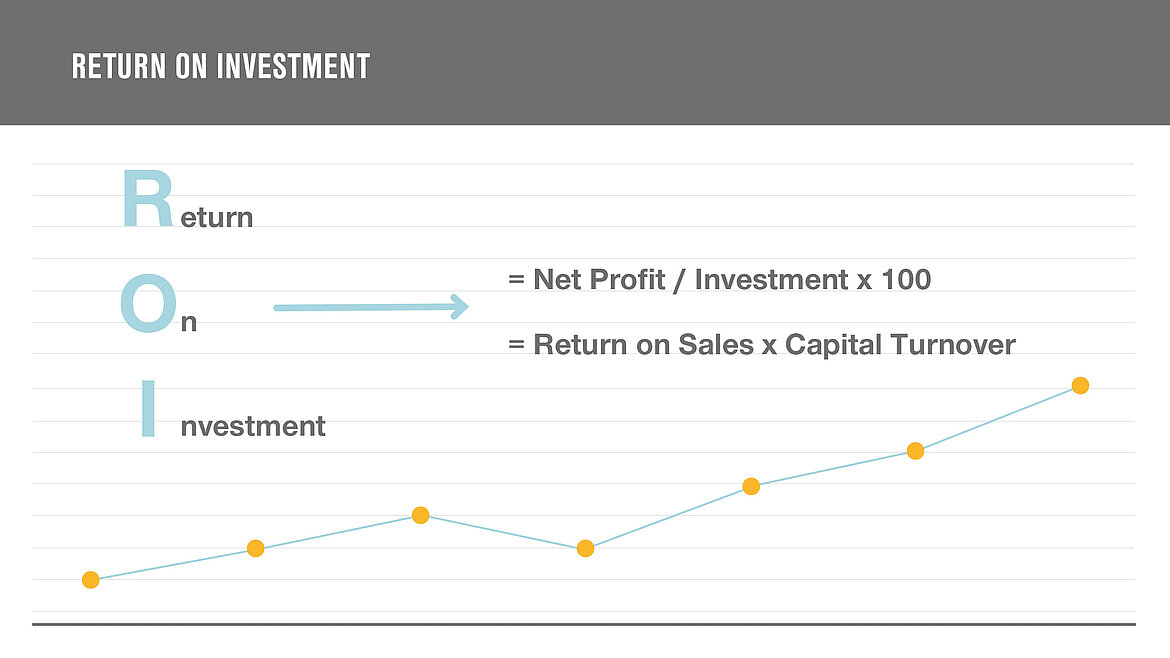
Return on Investment is ultimately based on the concept that all investments can be recouped through profit.
Only then was an investment, such as a new truck for the fleet, successful.
There are two options for calculating the ROI:
- (Profit/Investment) x 100
- Return on sales x Capital turnover
This gives rise to the ROI as a percentage value, which is ideally above 10 for a worthwhile investment. If the return on sales or the capital turnover increases, the return on investment inevitably also increases. This occurs due to increased sales or lower investment costs.
As a manufacturer of commercial vehicles or motor homes, how do you achieve this? Or how can a transport company or motor home rental company increase its return on investment? There are so many possibilities. One is to choose the right materials for the vehicles.
Effects of Material Selection in Production
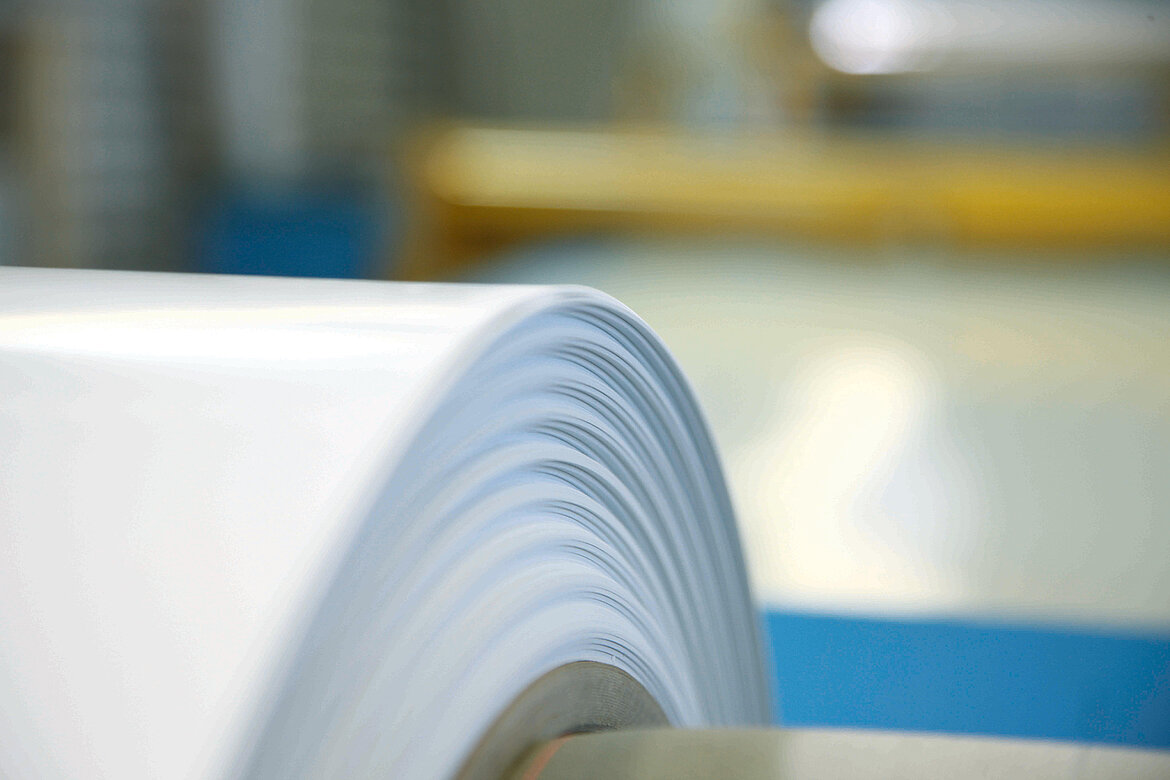
1. Warehousing
Storage space costs space, time and money. For this reason, the formats, sizes and quantities in which a raw material or product is received must always be considered for each material selection. Both aluminium and steel and GRP are available as large sheets, exact pre-cuts or as rolls. Depending on the structure and organization of the warehouse, one of these variants becomes interesting. However, the most space-saving is the roll form. As the construction materials for the cladding are very thin, a roll contains many linear metres with a comparatively small diameter. Upright next to each other, the material rolls take up less space than the same number of square metres of sheet material. GRP can also be wound easily into manageable rolls up to a thickness of 3 mm.
2. Processing
Sawing, drilling, riveting – Processing metal sheets is not rocket science and is familiar to unskilled workers. But do they know how to further process glass-fibre- reinforced plastics? Only commercially available tools are necessary. Another benefit: Cutting or sawing GRP does not create sharp edges as is the case with metals, where the processor can cut and injure himself.
In addition, a material must always be considered with other materials. So, how are aluminium, steel or GRP fastened to their beams? The metals are predominantly riveted. This can be done rapidly and requires little practice. In the long term, however, this creates weak points for corrosion and water ingress in the construction. Bonding prevents this problem and with short training, is just as easy to implement as conventional working methods.
In addition, it is always advantageous to save processing steps. This is possible with multi-purpose products. These are material qualities that already share several functions. For example, a wood-free floor construction made of woven-fabric-reinforced GRP with integrated PVC surface layer. Or interior cladding with a velour surface.
The 3-in-1 GRP LAMIfoamtex is an example of these products: A layer of glass-fibre-reinforced plastic forms the substrate. Above it is an individually adjustable foam layer as a soft core, with a thickness of between 2 mm and 8 mm. How hard or soft the end material is to be and what sound insulation is also required are the decisive criteria for selecting foam thickness and room weight. The top layer, which is also visible to the user, is a customer-specific decorative layer, such as artificial leather, fabric, velour or fleece.
However, the caravan or bus manufacturer has even more advantages. The three layers are bonded without adhesive using an innovative method. LAMIfoamtex is thus considerably lighter, more environmentally friendly and more sustainable than the conventional solutions that the vehicle manufacturer himself has to laboriously cover with fabrics. It also has an excellent sound-absorbing effect against noise emissions. LAMIfoamtex has a weight per unit area of 1.65 kg/m², while a plywood decor weighs approx. 2.4 kg/m² with a thickness of 4 mm. Even with an interior wall area of 18 square metres, the wooden composite would weigh 13 kg more than LAMIfoamtex. That is 30% of the weight per unit area. A shortened process chain is therefore only the beginning. It also saves labour, time, weight and material.
3. Production waste
To consider production waste, we must return to storage. This is because the materials already differ significantly from one another: Both aluminium and steel sheets and rolls are susceptible to transport and storage damage. These two materials can be bent and dented so easily that even a swing with a forklift or a dropped hammer can dent the sheet. A great deal of effort is then required to smooth the aluminium or steel. This is not always possible. GRP behaves differently: The plastic is shock- and impact-resistant so that even specific force does not permanently deform the material.
With aluminium or steel, in the worst-case scenario, impacts or knocks can even result in holes. These are then no longer invisible and cannot be repaired with the same functionality. Depending on the location and size of the damage, more or less material is wasted. If GRP is damaged by careless or improper handling, the area can be partially repaired by filling, sanding and painting. The gel coat with its protective properties can also be re-laminated during a repair.
Another factor for high production waste is edge pieces, pre-cuts or recesses that you can no longer use after the actual processing step. To save material, processing steps and disposal costs here, the material must be as accurate-fitting as possible. Individual custom-made lengths and widths make this possible. GRP manufacturer LAMILUX supplies its fibre-reinforced plastics tailor-made up to 3.20 metres wide and in any length. On the one hand, this prevents unnecessary waste and, on the other hand, it makes numerous pre-cuts unnecessary. This also prevents the sheets from hitting the finished surface, as they already use precisely fitting material.
Effects of Material Selection on Construction
The biggest trend in vehicle construction at the moment is probably lightweight construction. Regardless of whether for petrol engines or e-mobility: The lighter a vehicle, the better for the environment, image and running costs. Saving weight reduces the truck fleet operator's energy costs and allows the caravan owner a higher payload. At this point, aluminium and GRP, which are significantly lighter materials, win over steel. Should stability be a criterion, GRP is the overall winner.
However, despite its stability, even GRP cladding can suffer damage. Damage such as holes or cracks can be repaired easily and without the need to replace the material. The site is filled, sanded and then receives a new laminated gel coat or the site is painted – a little like open-heart surgery, but without the scars. This is not possible for aluminium and steel. The area is either visibly taped over, or the entire cladding part is replaced.
Effects of Material Selection on the Life Cycle
So many things happen during the life of a motor home or a truck. Above all, many things that cannot be predicted. Nevertheless, the right material protects the vehicle from external influences such as sun, water or mechanical stress. Because on the one hand, the appearance suffers from this, but on the other hand, so does the whole construction.
1. Water and moisture
Aluminium and steel are susceptible to corrosion and rust. A typical property of metals. We have all seen trucks with rusty old trailers. GRP does not have this problem: The glass fibres and resin used are corrosion-free. Metal suffers enormously from road salt in winter, but GRP is unaffected.
2. Hail, shocks and impacts
As with the processing of metals, it is similar in the life cycle of the vehicle: Aluminium and steel remain deformable. This means that both hail on the outer surfaces and impacts caused by loading and unloading can cause minor to major damage: Surfaces get bumps, dents or even holes that require complex repairs, if at all possible. GRP also prevails here in the selection of materials: The material is impact-resistant, robust and cannot be deformed by hail or impacts.
3. Sunlight and heat
If the outer surfaces fade after a few years or months or even become blistered or deformed due to heat, good advice is often expensive. Here, good materials differ from excellent ones, even within the material GRP itself. Compare the side walls of motor homes made of different GRP in the following two images after one or three years.
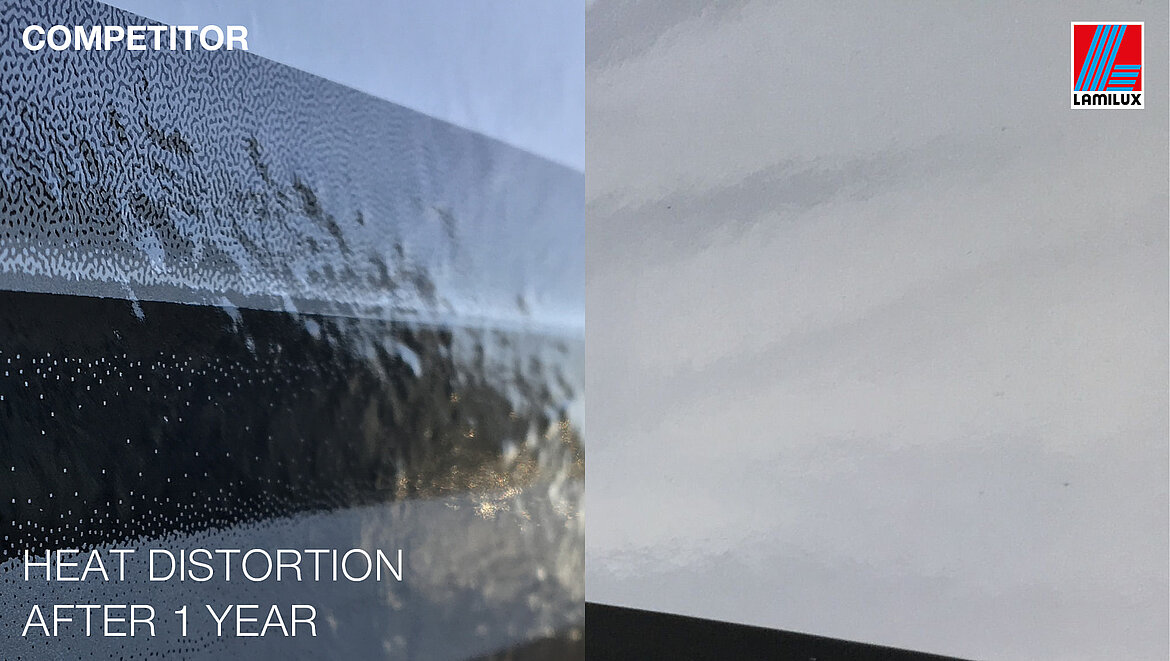
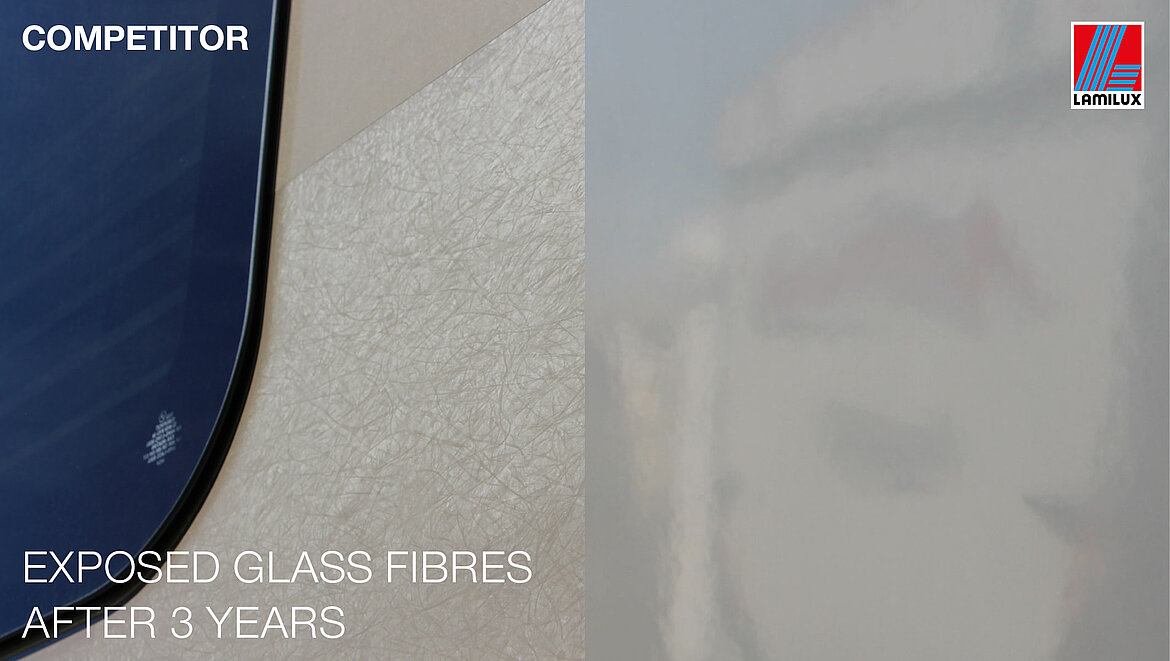
As you see: All GRP is not the same. Both the raw materials used and the quality and production technology make a major difference to performance, durability and appearance of fibre-reinforced plastics. This shows that even within a material family, there is still a great deal of choice and this has a significant impact on the life cycle of a vehicle.