Which material is easy to clean?
Who considers whether a product is easy to clean when they buy it? Other than when buying kitchen utensils? The fact that pots, pans and crockery should be easy to clean goes without saying, so we don't think about it again until the burnt on residue simply cannot be removed from the pan. And what is usually noticeable? Exactly: the surface finish. So, how does cleanability relate to the surface of the material?
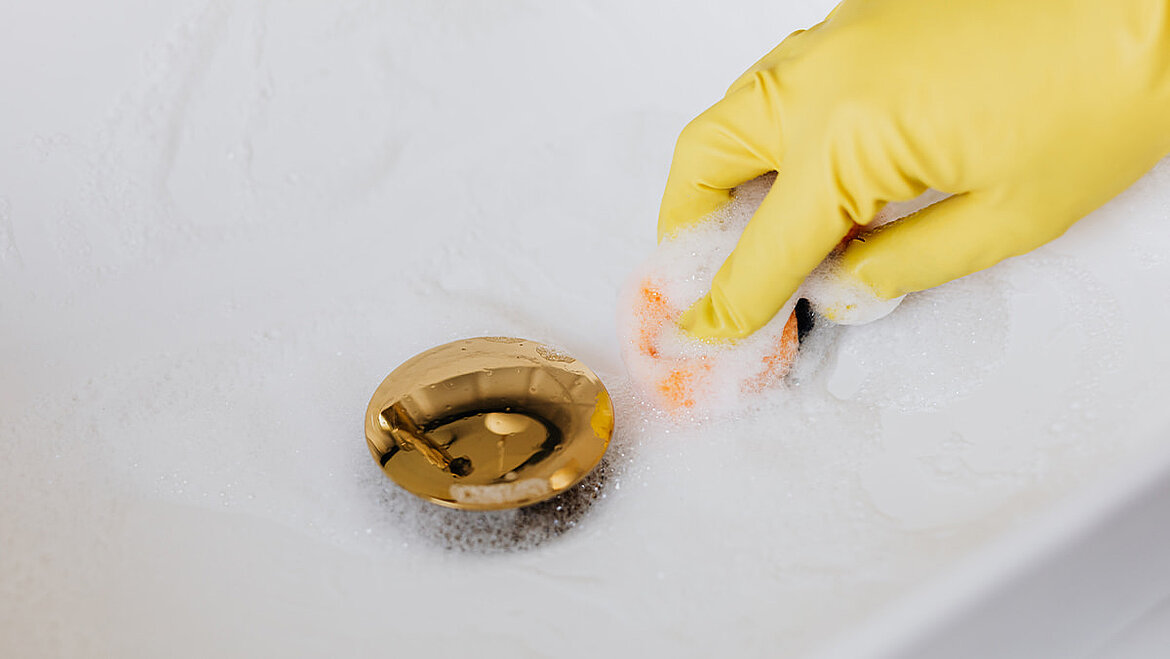
Another example: The house is ready to use, the bathrooms are new and the corner bathtub is resplendent in gleaming white. The surface of the bathtub is beautifully smooth and easy to clean. Dust and soap residues can be easily wiped away. But after decades of cleaning, the surface becomes rougher. Run your hand over it and the difference to a new bathtub is noticeable. The result: Cleaning is no longer as easy as it was ten years ago. But why?
Some bathtubs are coated with an enamel layer. This makes the surface so smooth. Over time and through regular cleaning, this coating is worn away.
The rough surface allows limescale and soap residue to adhere better. Which means greater effort is required to clean the rough surface. Aggressive cleaners are often used to make cleaning easier. However, these aggressive cleaners can increase the roughening of the bathtub surface. A prime example of how the roughness of a surface can make it more difficult to clean.
Surface energy and adhesion
Surfaces to which dirt does not easily adhere can generally be cleaned more easily. Pans with non-stick coating are a prime example of this. This coating is based on the composite polytetrafluoroethylene (PTFE), better known as Teflon™. This ensures that the surface behaves hydrophobically (ancient Greek: repels water or moisture). From a physical perspective, particle adhesion is related to surface energy. In principle, the lower the surface energy, the more difficult it becomes to wet the surface and it thus shows less adhesion. To the Teflon pan again: If you observe the behaviour of water in this pan, you can see that it rolls off. It dewets. The coating repels the water. It behaves hydrophobically due to the low surface energy. On the other hand, this phenomenon cannot be observed in an uncoated pan. Because an uncoated metal has a high surface energy and is therefore hydrophilic (ancient Greek for water lover).
And how can we describe the relationship between surface energy, roughness and wetting? Surface energy basically determines whether the surface behaves hydrophobically or hydrophilically. So it repels water or loves water. Roughness enhances this effect.
For the enamel coating of the bathtub, this means that the rougher the surface, the easier it can be wetted. Accordingly, dirt sticks to it more readily. Making it even more difficult to clean.
How easy is it to clean different materials?
Let's take a closer look at applications other than pans and bathtubs to take a more general look at the cleanability of material.
The following applies to all materials and material surfaces: Less adhesion also means less cleaning effort. Stainless steel, aluminium sheets and composites should serve as examples.
Stainless steel
Steel is a metal and therefore generally has a high surface energy, which promotes adhesion. This in turn makes surface cleaning more difficult. In order to reduce the roughness of the surface, there are various machining options, for example electropolishing. This reduces the micro-roughness of the metallic surface. The process is based on controlled electrochemical abrasion of the surface. Sulphuric acid and phosphoric acid are usually used for steel. However, the resulting reduced roughness also means more effort and higher costs. There is even more to consider when it comes to cleaning. Detergents can also promote corrosion of the steel and adversely affect the surface due to their acidicity or basic pH value. The consequence: Rust. Stainless steels are often used to increase corrosion resistance. However, there is still a risk of roughening due to the cleaning cycles. Powder coating or painting is therefore necessary to prevent corrosion.
Aluminium sheet
Aluminium is also a metal. Therefore, there is a similar problem here as with steel. Aluminium does not rust, but the surface can also be attacked by highly acidic or alkaline cleaners and roughened by corrosion. A prime example of corrosion of aluminium is pitting corrosion at contact points with other metals, e.g. when using steel screws. To avoid this, the aluminium sheet can be coated with a thin layer of paint. This not only reduces surface roughness, but also achieves lower surface energy, as the paints are often composite-based. Both the lower roughness and the lower surface energy reduce adhesion and thus facilitate cleaning. This also protects the metal against corrosion.
However, this thin paint coating can be damaged by knocks or scratches. Metal becomes exposed. Corrosion can now occur due to the combination of penetrating water and aggressive cleaner under the coating.
Composites
In terms of cleanability, composites are the ideal materials for areas where hygiene matters due to their low surface energy and low surface roughness. The material performs well, especially in food processing and storage, such as in cold rooms. The food industry has many requirements for the materials used and installed. Let's take a look at wall panels: Coated metal sheets are often used to manufacture wall panels, despite the risk of corrosion during constant use. This is due to their mechanical properties.
A brief summary of the metal problem: Generally, a high degree of roughness occurs here, which does not facilitate cleaning. The surface must therefore be refined. There is also a constant risk of corrosion from moisture and cleaners, so a coating should be used. The best way to do this is to use a composite-based paint to prevent corrosion. However, this paint can be damaged by impacts or scratches, which can lead to corrosion when cleaning.
Plastic, on the other hand, is corrosion-resistant and very easy to clean due to its surface properties. This means that the mechanical properties of metal sheets are not present. The best of these two materials combines glass-fibre-reinforced plastics (GRP). By combining glass fibres with a composite matrix, GRP sheets offer mechanical properties at the level of aluminium sheets and steel sheets - or even better. Gel coat is applied to the sheets as the finish. This is fibre-free and with a seamless transition into the laminate – in contrast to coatings. The smooth composite surface created in this way offers particularly low adhesion to dirt, is easy to clean and resistant to detergents. For additional safety – especially in the food processing sector – there is a LAMILUX Gelcoat which is HACCP-certified for direct long-term contact with meat under cooling conditions. It can also be equipped with antibacterial nanosilver, which ensures additional safety even between cleaning cycles.