Depending on the GRP manufacturer, the fibre-reinforced composites are available as individual sheets or as coils – or even both. LAMILUX Composites has both methods of delivery in its repertoire and individually adapts the sizes and lengths to customer requirements. However, this means that, as a customer, you need to know your needs. Much more: you need to know whether sheets or coils better meet your storage and production needs and what dimensions are suitable for further processing in your production. LAMILUX can then produce composite sheets up to 3.2 metres wide and up to 12 metres long for you. Up to 300 metres of GRP, which varies in thickness from 0.3 to 3.0 mm, can fit on one coil. Sheets can be up to 5.0 mm thick. The production method is the same for all these variants: the fibre-reinforced composites are produced on continuous flat sheet production lines with consistently high and reproducible quality at all times. This means that the thickness, colour and composition within a sheet or coil, as well as the next batch, are always identical.
The advantages and disadvantages of GRP as coils
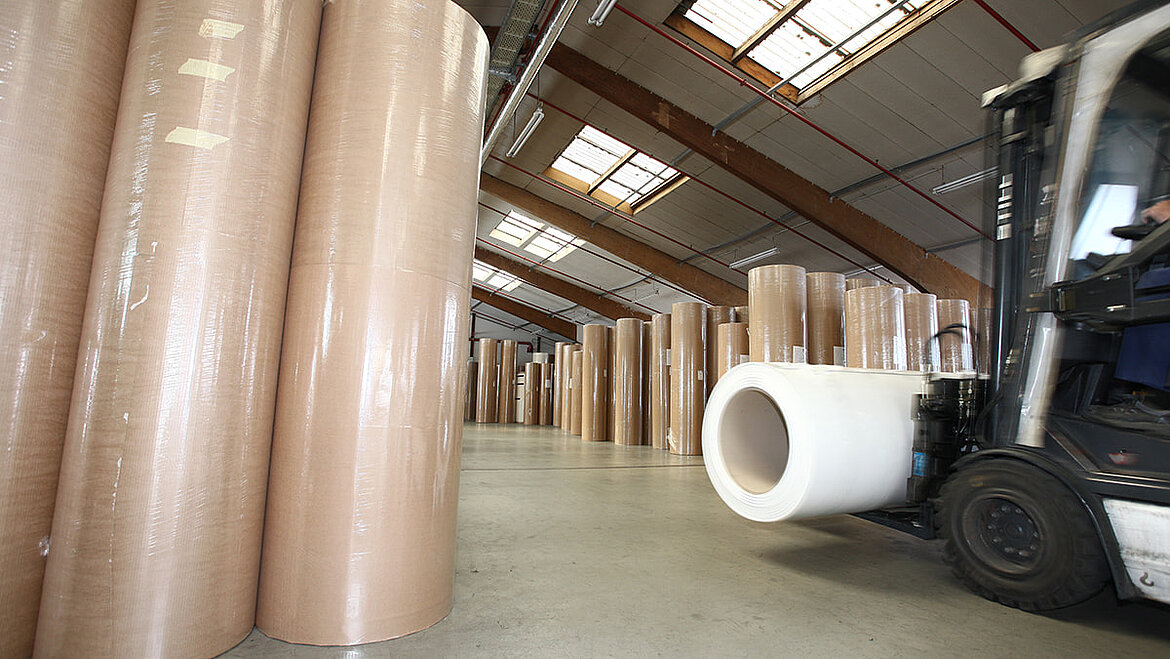
If the decision is made to use GRP as coils, this is particularly noticeable in the storage capacity. As a rule, the coils are stored upright, which takes up significantly less space than the same amount of GRP in horizontal sheets. This is not only noticeable during storage, but also during transport: significantly more GRP coils than sheets fit into a truck. This reduces storage costs as well as transport costs. GRP coils can also reduce costs in your own production. The width may be fixed, but the length of the cut can be freely selected, allowing pieces to be tailored depending on the application. This saves oversized cut-offs and unnecessary waste. However, GRP already offers price savings when purchasing as coils: as the GRP manufacturer no longer needs to cut to size as with GRP sheets, the price per metre can be reduced.
However, this argument can cause other costs in further processing: on the one hand, you need to integrate additional work steps into your processes in order to cut the desired GRP length on site yourself. You will also need special tools and equipment such as a pre-cutting machine, pre-cutting tool, unwinding device and equipment for coil handling such as a coil gripper or a forklift.
Another disadvantage of GRP as a coil can be if a raw-material-related defect appears at an unfavourable point in the material – such as a mat defect or a gelcoat defect. This can result in more waste if this piece needs to be cut out.
Finally, an important criterion for choosing sheets or coils as the delivery form for glass-fibre-reinforced composites is how thick the material should be for your application. LAMILUX GRP, for example, can produce thicknesses of up to 5.0 mm, but composite sheeting can only be rolled up to a maximum thickness of 3.0 mm due to its high inherent rigidity. However, there are also materials with even higher inherent stiffness, meaning that this can only be wound up to a thickness of 2.0 mm.
The advantages and disadvantages of GRP as sheets
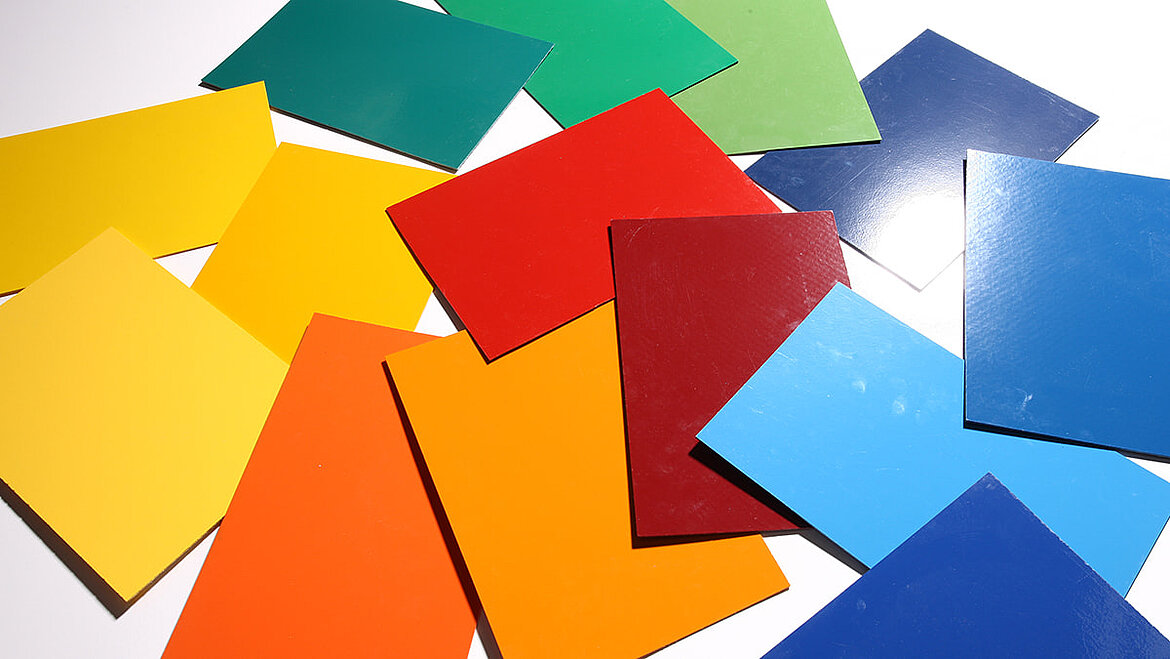
The advantages and disadvantages of GRP as sheets arise from the advantages and disadvantages of GRP as coils. Here they are again in detail:
Clearly a pro-argument for GRP sheets is that they are ready to use. As a processor, you tell the GRP manufacturer the exact dimensions in which you need the composite sheets. You can then use the sheets that have been tailored to your application directly in your production. This saves you effort and process steps on the one hand, and also additional investments in tools and equipment for cutting to size. The thickness of the GRP is also adapted to your requirements for composite sheets. In contrast to coils, there is no limitation here that arises from the winding process.
GRP that is thicker than 3.0 mm is too stiff to roll. For sheet goods, the thickness does not matter. LAMILUX therefore manufactures GRP sheets up to 5.0 mm thick. This results in particularly strong, rigid and robust composite sheets, which are used in applications with extreme requirements – for example in facade panels or enclosures.
However, the greatest advantage of GRP sheets may be their manageable size, which is why potential faults in the material are identified directly by the manufacturer LAMILUX and the sheets are sorted out. On the other hand, in the case of coils of several hundred metres, there may be occasional minor faults in the material, which can then only be eliminated during further processing.
Nevertheless, there are also disadvantages with delivery and storage in sheets. If the production process requires different lengths at short notice, GRP sheets are inflexible. In this case, you only have the options of connecting two sections, if the application allows, or placing a new sheet order with adapted dimensions. The question is then: do the storage capacities allow for this? GRP requires considerably more storage space if it is stored in sheets instead of in coils. Every additional order makes this disadvantage all the more visible.
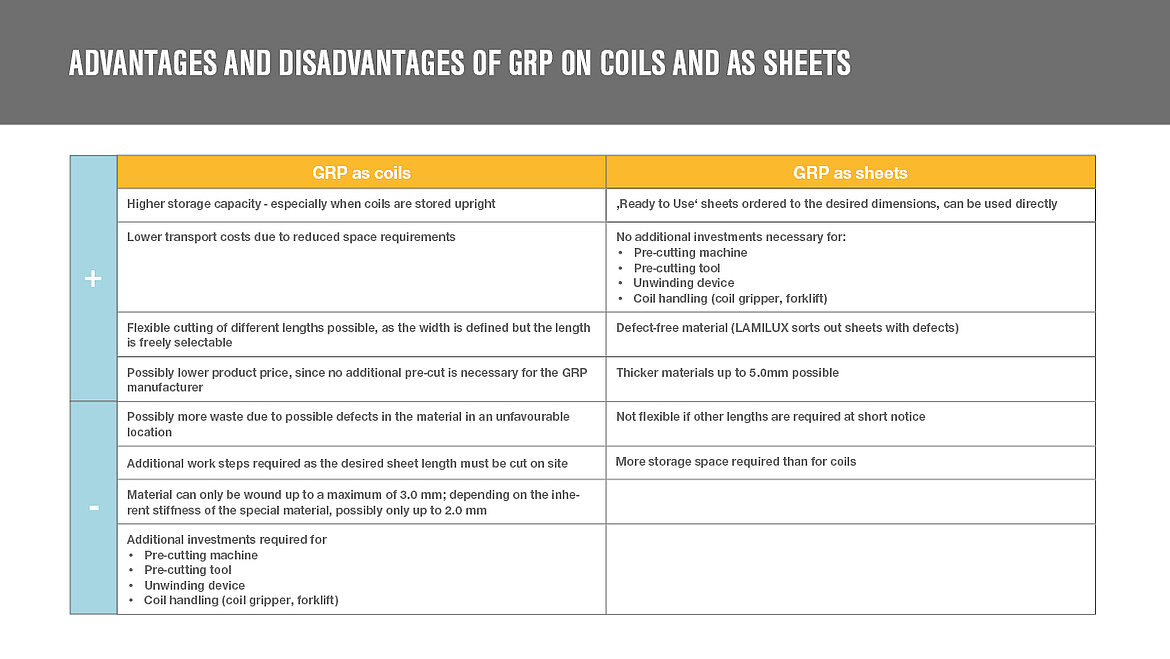
Which factors are still important when selecting GRP?
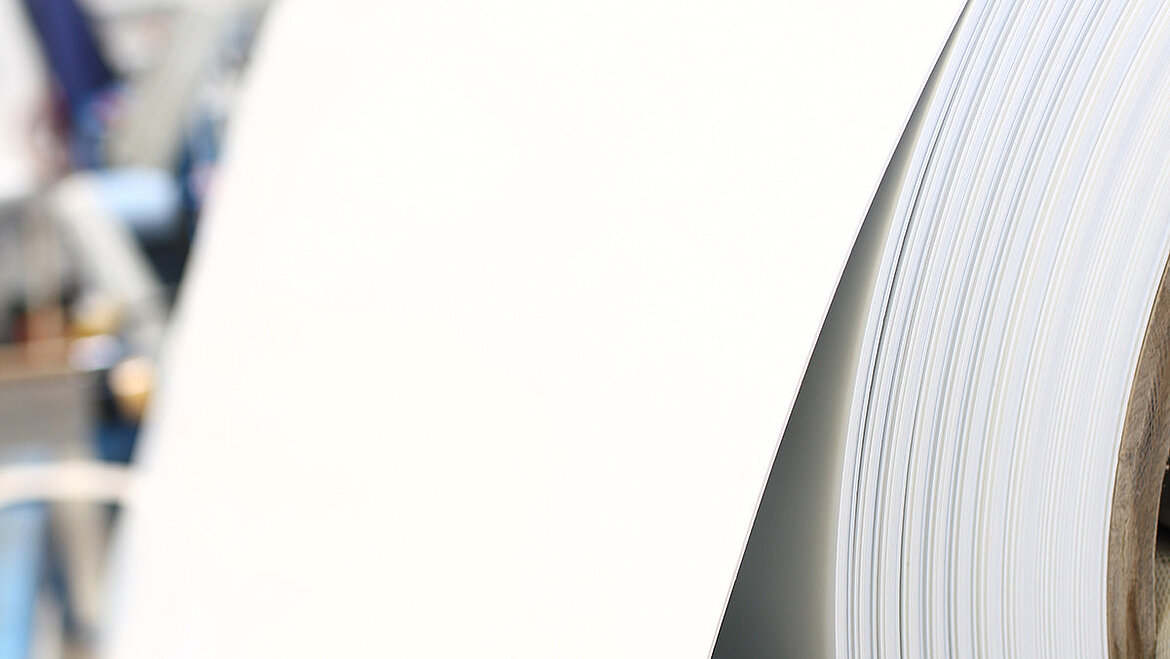
In order to ultimately find the right GRP product – i.e. the right delivery form and the right material composition – for your own production, you should compare the various manufacturers in four categories: costs, service, reliability and quality. Costs mainly include the criteria already mentioned above in this article: the material price itself, scrap and waste, storage and transport costs as well as the costs for coil or sheet replacement in further processing. In service, everything revolves around the additional services that the GRP manufacturer offers beyond the product itself. Criteria here are, for example, the importance of tailor-made product samples, delivery times, response time to problems and questions, support in application technology, delivery quantities, innovative power and the characteristics and size of the product portfolio.
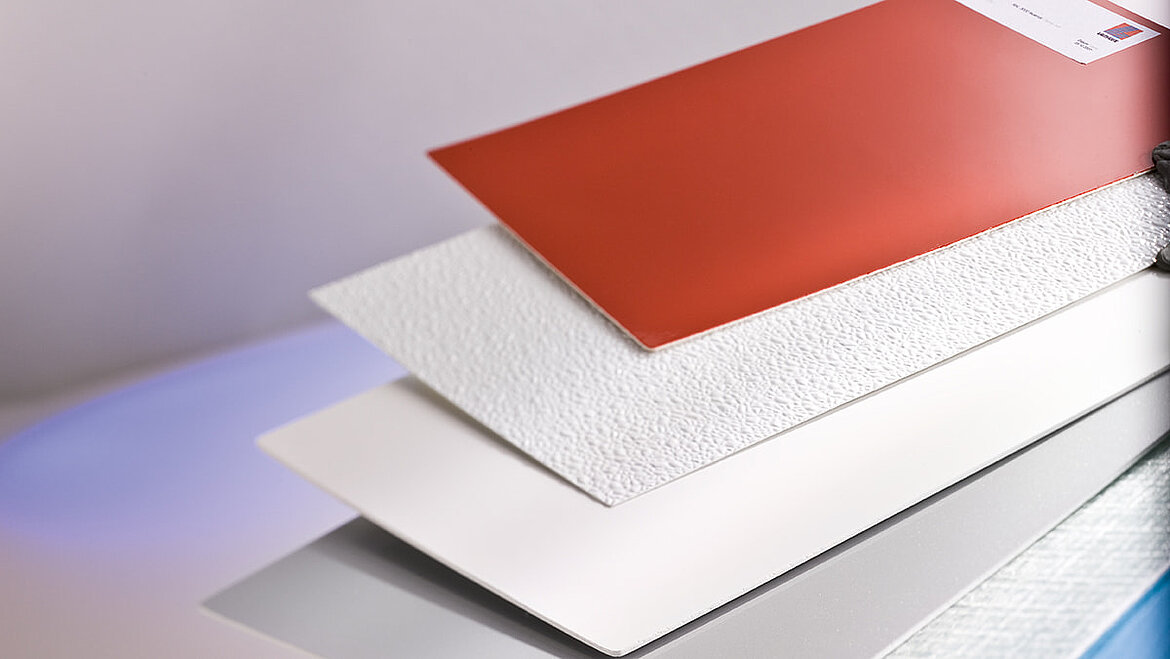
LAMILUX also offers product samples of all its GRP materials. You can order these free of charge on the corresponding product pages. You also need to be able to rely on your supplier. Are the agreed delivery quantities and times fulfilled? Does the product quality remain consistently high? Quality is also the fourth key word: What is the general product quality? Some manufacturers also have the quality of their production processes and laboratory tests certified by independent testing institutes. Such certificates provide a lot of information about the final GRP product. LAMILUX's TÜV-certified test methods are an example of this. LAMILUX is the only GRP manufacturer in the world to have 17 of its partially developed material and process tests certified by TÜV Süd and is therefore subject to strict quality standards.
GRP in sheets or coils – Conclusion
A clear winner cannot be determined when comparing GRP sheets to GRP coils – the areas of competition are too diverse for this. Both forms of delivery and storage have their advantages and are recommended for different areas of application.